Services
Technical Services
Technical Services
Contact our experts today for all your product and installation questions.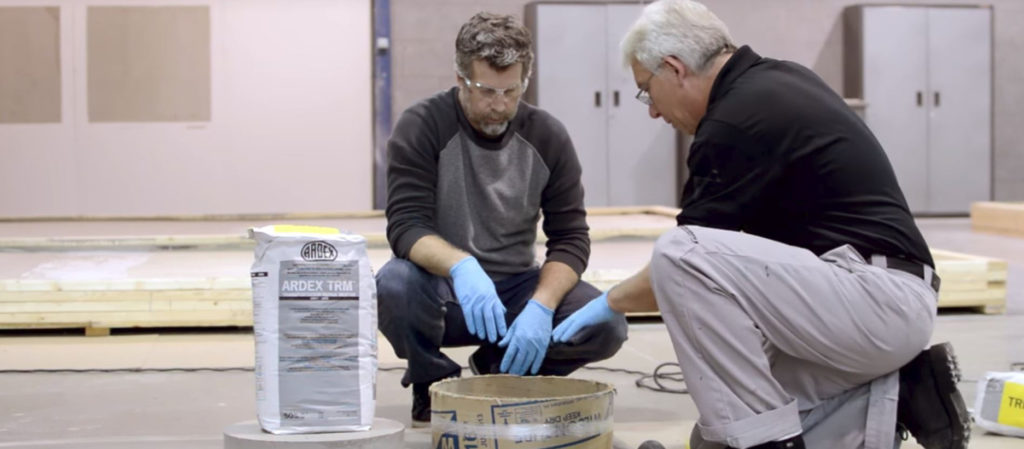
ARDEX has the most reliable and experienced technical service professionals in the industry. ARDEX Technical Service Consultants are available on the phone from 8 a.m. to 5 p.m., Monday through Friday, EST, or in the field. Your local ARDEX Americas Sales Professionals and Technical Field Specialists provide a guaranteed 24-hour jobsite response time. The ARDEX Americas Technical Services Team provides product and installation recommendations based on decades of experience. Technical recommendations can be provided in writing when required for all types installation environments.
ARDEX Technical Services phone:
1 888 512 7339
ARDEX Technical Updates:
- Cold Weather Precautions for ARDEX and HENRY Products
- Warm Weather Installation Guidelines
- ARDEX Products and Dew Point
To learn more about our technical department, scroll down to meet our technical team. You can also learn about OSHA/Silica standard compliance and read about our philosophy, Proper Prep.